Fire resistant matrix materials for use in aircraft composites and cabin interior applications
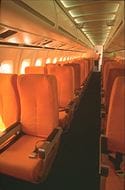
The Federal Aviation Administration (F.A.A.), USA, has recently initiated a research program to develop low-cost, environmentally-friendly, fire resistant matrix materials for use in aircraft composites and cabin interior applications. The flammability requirement for new materials is that they withstand a 50 kW/m2 incident heat flux characteristic of a fully developed aviation fuel fire penetrating a cabin opening, without propagating the fire into the cabin compartment. The goal of the program is to eliminate cabin fire as cause of death in aircraft accidents. However, voluntary adoption of the new materials technology by aircraft and cabin manufacturers requires that it be cost effective to install and use, so it is expected that these new aircraft materials will be broadly applicable in transportation and infrastructure where a high degree of intrinsic fine resistance is needed at low to moderate cost. To this end the F.A.A. is evaluating a new, low-cost, inorganic geopolymer matrix derived from the naturally occurring geological materials- silica and alumina. At irradiance levels of 50 kW/m2 typical of the heat flux in a well developed fire, glass- or carbon-reinforced polyester, vinylester, epoxy, bismaleinide, cyanate ester, polyimide. phenolic, and engineering thermoplastic laminates ignited readily and released appreciable heat and smoke, while carbon-fiber reinforced geopolymer composites did not ignite, burn, or release any smoke even after extended heat esposure.
In the recently updated book Geopolymer Chemistry & Applications the fire and heat resistant composite applications are thoroughly outlined in Chapter 21. You may also go to the Geopolymer Library and download several papers..
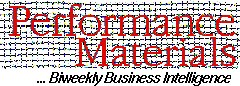
Excerpt from the technical press
Performance Materials,
February 5, 1996, page 5.
As Hot as You Like It
Mechanical Properties are Looking Good for French Inorganic Polymer that Doesn’t Burn.
Fire safety is a concern often voiced by those who are skeptical about the use of composite materials in the infrastructure. These fears may be put to rest by a revolutionary European matrix material that doesn’t burn at all (PM, July 31, 1995). “Fire is going to be the limiting criterion in a lot of infrastructure applications C says Rich Lyon of the Federal Aviation Administration (FAA) Tech Center in Atlantic City. But his ICCI ‘96 presentation about the new family of inorganic polymer composites was almost anticlimactic. “It’s a fairly boring story because there is no fire response,” Lyon said in Tucson.
FAA Is Interested, Too
The inorganic polymeric materials are cheap, at about $2-3 a pound. They cure at low temperatures.
And now there is evidence that the new material family, trade named Geopolymer (or, more precisely, Géopolymère), boasts mechanical properties comparable to those of organic-matrix composites. FAA-supported testing was conducted at Rutgers University in New Jersey.
“The initial results are very encouraging: Prof. P (Bala) Balaguru of Rutgers said at the Tucson infrastructure meeting. Carbon-matrix composites made with the Geopolymer matrix demonstrated a strength of approximately 327 MPa (about 225 ksi), he said, quite comparable to organic composites. “The same thing is true for flex and shear;’ Balaguru said. The Rutgers test coupons were made using 3K, polyacrylonitrile-based carbon fiber that was manually impregnated and vacuum-bagged for curing in an 80°C (176°F) heated press. The samples were post-cured in an 80°C oven for 24 hours.
Experimenters have thus far made samples only via hand layup, and have been able to achieve fiber loadings of only 50 % (the Rutgers tests were conducted on 45-percent material). At least 60 % is expected when fabrication processes are refined, says the FAA’s Lyon. Problems with voids are also expected to be solved when better fabrication techniques are applied.
“These materials are in their infancy) FAA Lyon says. Geopolymer inventor Joseph Davidovits spent much of his career as a textile chemist and began pursuing inorganic polymers in part, he says, behind a tragedy in France in which the deaths by fire of more than 100 young night club patrons were attributed to fast-burning polyester curtains. Davidovits cites three key Geopolymer attributes his company says “make them superior to ceramics, plastics, and organic composite materials:” (Performance Materials, February 5, 1996).
The First Non-flammable fabric laminate for Aircraft cabin and cargo interiors, Géopolymère Composite™ was introduced on November 18, 1998, in Atlantic City, NJ, USA, at the International Aircraft Fire and Cabin Safety Research Conference sponsored by the Federal Aviation Administration. More details in Press Release (see page 3)
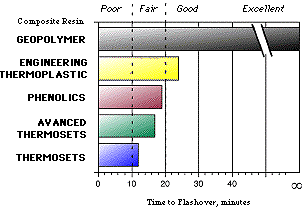
Predicted time to flashover in ISO 9705 corner/room fire test with various structural composites as wall materials
Press Release, November 20, 1998
The First Non-Flammable Material for Aircraft Cabin Safety presented at FAA.
Fire Safety Meeting in Atlantic City, New Jersey, USA
The First Non-flammable fabric laminate for Aircraft cabin and cargo interiors, Géopolymère Composite™ was introduced on November 18, 1998, in Atlantic City, NJ, USA, at the International Aircraft Fire and Cabin Safety Research Conference sponsored by the Federal Aviation Administration.
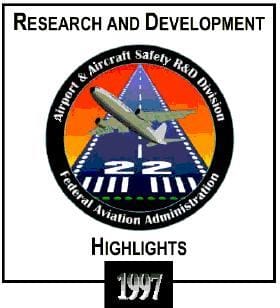
Current aircraft design utilizes several tons of combustible plastics for cabin interior components that includes the passenger compartment, cockpit and cargo compartments. This is a fire load comparable to the equivalent weight of aviation fuel. The recent introduction of fly-by-wire control system as well as the increase of electronics components on an aircraft (such as flat panel displays for TV, telephones and computers) represents a new, higher risk of electrical fires and the potentially tragic consequences of uncontained in-flight fires. The FAA is working to eliminate cabin fire as a cause of death in aircraft accidents. In the unusual event of an aircraft accident, there are only seconds for passengers to escape before toxic fumes and fire fill the cabin compartment.
The FAA flammability requirement for new materials is that they must withstand the 50-kw/m2 incident heat flux characteristic of a fully developed aviation fuel fire that penetrates the cabin skin. The material must prevent propagation of the fire into the cabin compartment. The first material to withstand this arduous test is Géopolymère Composite™ developed by Professor Joseph Davidovits of the Geopolymer Institute in France. Géopolymère Composite™ is described as an inorganic polymer (a silico-aluminate polysialate polymer) derived from the naturally non-flammable occurring geological materials silica and alumina, hence the name Geopolymer or Géopolymère in French.
Since January 1994, the Federal Aviation Administration has conducted a research and evaluation program on carbon fiber reinforced Géopolymère Composite™. Tests were carried out at the FAA Fire Research Section, FAA Technical Center, Atlantic City, NJ and at the Department of Civil Engineering, Rutgers, The State University of New Jersey, in collaboration with Prof. Davidovits’ French company, CORDI-Géopolymère SA, Saint-Quentin, France. The FAA experiments indicate that even after exposure to a severe fire environment (more than 1,500°F during several hours), the carbon fiber reinforced Géopolymère Composite™ retained 63 % of its original flexural strength of 245 Mpa (approximately 169 ksi). In comparison, all materials presently used in an aircraft, including aluminum sheets and parts, organic based laminate composites and plastics, actually burn and are destroyed when submitted to the same severe fire environment.
Aircraft operators and manufacturers are sensitive to cost and cost-effectiveness. Aircraft operators estimate that each pound of weight on a commercial aircraft costs between $100 to $300 in operating expenses over the service life of the aircraft. Consequently, fire safe materials for use in aircraft must be extremely lightweight. With its low density of 1.85, carbon fiber reinforced Géopolymère Composite™ is lighter than aluminum (density 2.70) and structural steel (density 7.86).