GEOpolymeric Cements for Innocuous
Stabilisation of Toxic EleMents
Geosynthesis of Rock-based Geopolymer cements was the objective of the European multidisciplinary BriteEuram industrial research project GEOCISTEM. The project titled cost effective GEOpolymeric Cements for Innocuous Stabilization of Toxic EleMents, in short GEOCISTEM, started on Jan. 1994 and has been completed on June 1997.
In J. Davidovits’ book, Geopolymer Chemistry & Applications, Chapter 10 is dedicated to Rock-based Geopolymer cements.

The project seek to manufacture economical geopolymeric cements primarily for the long-term containment of hazardous and toxic wastes and for restoring sites highly contaminated with uranium mining waste (the WISMUT sites in former East Germany). The patented GEOPOLYTECH® process is currently undergoing industrial testing on various sites. In the recently updated book Geopolymer Chemistry & Applications this application is outlined in Chapter 26. You may also go to the Geopolymer Library and download several papers.
Rock-based Geopolymer cements are manufactured in a different manner than Portland cement. Geopolymeric cements do not require high temperature kilns, or large expenditures of fuel, nor do they require such a large capital investment for the plant and equipment. Thermal processing at temperatures not higher than 600-700°C of naturally occurring alkali-silico-aluminates and alumino-silicates (geological resources available on all continents) provides suitable rock-based geopolymeric raw-materials.
In addition, the GEOCISTEM technology reduces the energy consumption of manufacturing cement. The global introduction of these low-CO2 geopolymeric cements, for civil engineering, infrastructure and general construction purposes will reduce the CO2 emissions created by the cement concrete industry by 80%. This can mitigate overall Global Warming .
Partners:
- European Commission, Brussels
- B.R.G.M. Bureau de Recherches Géologiques et Minières (France)
- CORDI-GEOPOLYMERE SA (France)
- LAVIOSA CHIMICA MINERARIA SPA (Italy)
- CAGLIARI UNIVERSITY, Dpt Scienze della Terra (Italy)
- BARCELONA UNIVERSITY, Facultat de Geologia (Spain)
Sub-contrators for Cordi-Geopolymere SA, Saint-Quentin:
- WISMUT GmbH, Chemnitz (Germany)
- HEIDELBERGER ZEMENT AG, Heidelberg (Germany)
- NAMUR University, Namur (Belgium)
CEMENTI BUZZI, Torino (Italy) - CAEN UNIVERSITY, Centre Etude et Recherche sur l’Antiquité (France)
- Project leader: Prof. Dr. Joseph Davidovits, Cordi-Geopolymere SA
Acid Resistant Concrete for Uranium and Metallic Mining Sites
Metallic mine tailings are usually generating sulphuric acid that results from the oxidation of pyrite. The resistance to strong sulphuric acid solution (5% H2SO4 solution) was investigated after the standard 28 days of hardening. Testing involved comparative sand mortar standard methods with Portland cement (type I 42.5 R from our sub-contractor Cementi Buzzi) and a geopolymeric cement that comprises 75% by weight of geological elements. This cement is coined CARBUNCULUS cement™ because of it similarity with the calcined pozzolan “carbunculus”, which according to the Roman architect Vitruvius (1st Century AD) was the basic material of the good Roman mortar (see in Archaeo-Analogues and also the paper #D Searching for Carbunculus ). After 60 days, CARBUNCULUS cement remains practically intact whereas the acid corrosion has destroyed more than 65% of Portland Cement I.42.5 (weight loss and change in shape and volume).
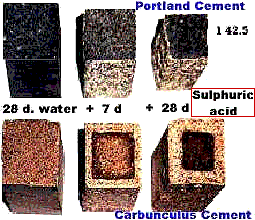
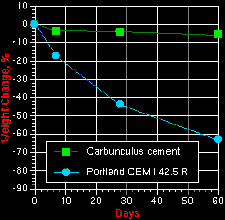
Comparative test CARBUNCULUS cement™ vs. Portland cement I.42.5, 28 days of hardening. Weight loss after 7, 28 and 60 days in Sulphuric acid solution (5%, pH=0).